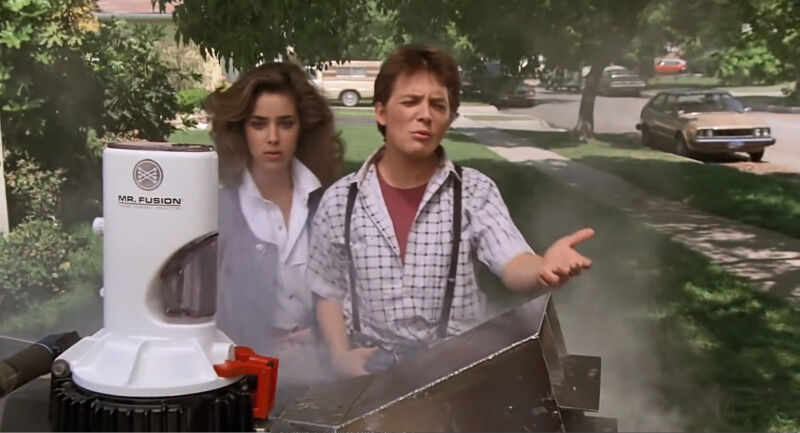
It’s hard to write about battery research around these parts without hearing certain comments echo before they’re even posted: It’ll never see the market. Cold fusion is eternally 20 years away, and new battery technology is eternally five years away.
That skepticism is understandable when a new battery design promises a revolution, but it risks missing the fact that batteries have gotten better. Lithium-ion batteries have reigned for a while now—that’s true. But “lithium-ion” is a category of batteries that includes a wide variety of technologies, both in terms of batteries in service today and the ones we've used previously. A lot can be done—and a lot has been done—to make a better lithium-ion battery. In fact, gains in the amount of energy they can store have been on the order of five percent per year. That means that the capacity of your current batteries is over 1.5 times what they would have held a decade ago.
Lithium-ion batteries have evolved, whether you noticed or not. Here's how.
Why does the Li-ion roar?
It’s helpful to start by defining what makes a battery “lithium-ion.” The stars of the show are obviously lithium atoms, which give up an electron easily to form ions. Every battery has a cathode and anode, with a separator and electrolyte sitting between the two. On the cathode side, lithium is found in a metal oxide compound, where it will stay as long as each atom is holding that electron. Once separated from the electron, lithium ions will move across the separator to collect at the anode. The freed electrons can’t cross the separator, so instead they move through whatever circuit is connected to the battery’s two electrodes.
During charging, lithium ions and electrons accumulate in the anode. During discharge, electrons flow through the circuit and lithium ions move through the separator again, reuniting as lithium settles back into the structure of the cathode material.
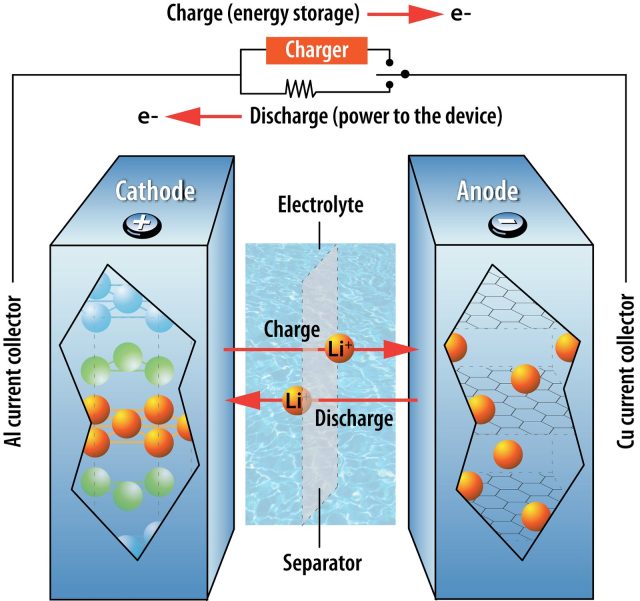
An actual battery is formed from three layers of materials: cathode material deposited on a metal foil, the separator layer, and anode material deposited on another metal foil. Stack these flat, and you have a pouch- or prismatic-style battery like you might find in your phone or a Chevy Bolt. Roll the layers up in a coil, and you have a cylindrical battery like those in power tools or a Tesla.
You can’t get rid of the lithium and still call this a lithium-ion battery, but everything else is fair game. There are many different materials used for the cathode, and you can change the separator or try another chemistry for the electrolyte. There are even options for the anode material, though one has dominated for a long time.
Early attempts at lithium-ion batteries tried using solid lithium metal for the anode, but this produced serious stability problems. (Problems that are still being worked on today.) The breakthrough was the use of graphite for the anode. Graphite consumes valuable space while not contributing additional energy capacity, but its sheet-like structure gives lithium ions safe housing while greatly improving cycle life and safety. This enabled the first Sony lithium-ion batteries in 1991.
Even the first lithium-ion batteries had greater energy density than nickel-metal hydride batteries, holding more charge in less space while weighing less. They also operate with a higher cell voltage, which can be useful. Of course, it’s not all sunshine and unicorns. Lithium-ion batteries are more expensive, and the organic solvent used for the electrolyte is flammable, creating a fire risk that must be carefully managed.
Nickel-metal hydride batteries continue to be used in rechargeable AA and AAA batteries, as well as hybrid vehicles that don’t need as much energy storage. But the lithium-ion battery dominates where space and weight is at a premium, in places like a laptop or electric vehicle.
A very particular set of skills
Batteries have more than one or two important characteristics, and so they are often represented by a spider chart (like the one below). “There’s energy density, there is power density, there is cost, there is cycle life, there is calendar life, there is safety,” Argonne National Laboratory’s Venkat Srinivasan told Ars. “What typically happens is that, in batteries, it’s a compromise of these different things.” Even just sticking to lithium-ion batteries, there are configurations and designs that can emphasize certain of these characteristics at the expense of something else. Energy density could be boosted a bit, for example, but maybe it comes at a higher cost or with a reduced cycle life.
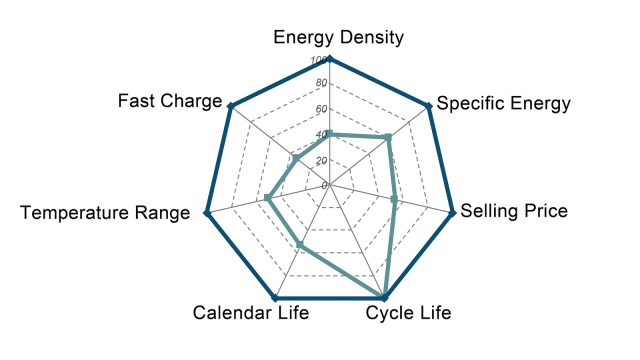
This may be one of the causes of the frustration or skepticism directed toward news about battery research. A study may identify a way to significantly improve one characteristic, generating an exciting top-line conclusion. But the design may be impractically poor in some other way. While battery researchers learn from what does and doesn’t work, this means that a lot of laboratory batteries you may read about will never hit the market.
However, this also means there are a lot of knobs that can be used to customize a specific battery design. Even seemingly subtle things, like the exact thickness of the anode or cathode layer that gets deposited on its metal foil, can affect behavior. The thicker the cathode relative to its foil backing, for example, the greater the energy density of your battery, since less of the total volume is taken up by the foil. But a thicker material layer also means a longer journey for lithium ions and electrons. That generates more heat during battery operation and leads to shorter cycle life. Keep the cathode thinner, on the other hand, and it can handle higher charge and discharge rates, since the shorter journey is easier.
In small devices, where space is at a premium, more expensive designs that maximize energy density are preferred. Electric vehicles are different, since the cost of the battery is a large portion of the overall price—adding a 20 percent premium to the battery could easily push a car beyond your budget. Cycle life has to be much greater, too. Reduced battery life in a phone after two years is generally viewed as par for the course these days. Significantly reduced battery life in a car after two years would be a deal-breaker.
Since electric vehicles are currently on the edge of affordability and (at least for some) acceptable range and charge time, small battery improvements are much more visible here.
Engineering, status report!
Lots of those improvements relate to the engineering of the whole battery system, rather than changes to the chemistry of the battery itself. This stuff is much less likely to make news (do not wait for my upcoming story titled “Car manufacturer reduces copper in new model by 1.8 percent!”), but a lot of little things add up.
Some of this has to do with reducing the materials that aren’t the anode or cathode or electrolyte. “We’ve also been cutting back on the thickness of the separator material we are using,” Srinivasan said. “It used to be... 25 microns thick and today it’s... 12, 13 microns thick […] The copper and aluminum foils we use to pull current out of the battery—again, it’s not an active component, they don’t store energy, but you need them to get the current out. We’ve been making them thinner and thinner so that we can minimize extra weight and volume in the battery.”
The form factor of the cell package can be optimized for cost and performance, as illustrated by Tesla’s iterations on the size and construction of the cylindrical cells they use.
Particularly for vehicles, the total battery pack is far more than just one cell. Like the battery chemistry, it’s very much a balancing act—part tetris, part safety, part performance. Some electronic devices eschew a standard rectangular pouch battery for complex shapes that take advantage of any available space, for example. Vehicles can present a similar space-filling puzzle, although early designs that packed in batteries here or there largely gave way to flat “skateboard”-style packs that can be used as structural components. Even there, the simpler the pack, with minimized packaging and wiring, the more storage you get per cubic foot (and per dollar).
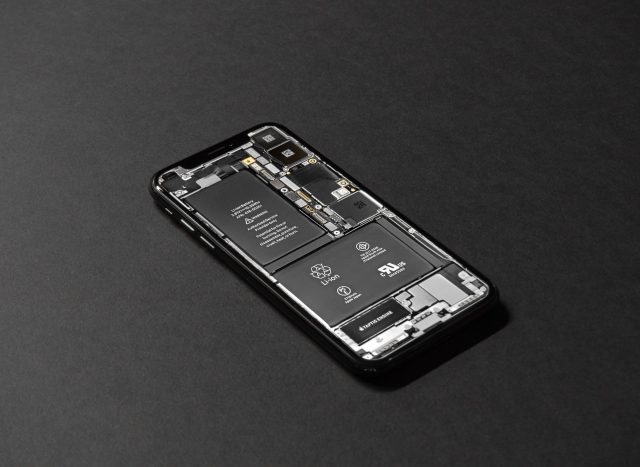
One key to safety, performance, and longevity is temperature management. Most electric vehicles actively warm the pack for charging when it’s too cold, and they cool the battery pack as it generates heat. That helps prevent the fire risk and reduces capacity degradation. Along with configuring higher voltages, it also allows for high charge rates.
“The more energy you put in a tight space, the more you have to pay attention to your thermal management,” Argonne National Lab chemical engineer Andrew Jansen explained. “One of the nice things about lithium-ion systems is they’re very energy-efficient. Your energy efficiency is often around 94 to 95 percent, but that still means you have 5 percent of wasted energy when you charge off the battery.” That wasted energy ends up as heat, which can damage battery components if not managed properly.
Some things—like faster charging—might be easy to notice in use or highlighted in a product’s marketing. Since companies tend not to give out detailed technical specs (especially if they're not the ones making the battery), critical functions like thermal management or cell-level charge-balancing tend to fly under the radar. But improvements at the battery pack level have necessarily occurred alongside improvements inside the cells.
Real chemistry between these two
The anode side of the cell has afforded less freedom for tailoring batteries to different needs. Graphite has been the only safe solution—so far. Using silicon for an anode has been almost as tempting as the old lithium-metal design because it holds a lot of lithium; a silicon anode would be 10 times more energy dense than graphite. But loading up a silicon anode with lithium atoms as you charge the battery causes it to expand by around 300 percent, causing obvious problems.
Nonetheless, silicon is increasingly appearing in batteries. Incorporating just a few percent silicon in your graphite anode bumps up the energy density slightly without the destructive side effects. “You take a graphite that gives you about 340 milliamp-hours per gram,” Jansen said, “and with a little bit of silicon in there, that graphite-silicon combination will give you, say, 400 or 450 milliamp-hours per gram.”
“If you add too much silicon, the battery will collapse,” Srinivasan told Ars. “So what companies are doing is they’re tweaking and adding a little bit more silicon every year, learning how this behaves, trying to make it better, and ultimately getting it to a stage where you can get the increased energy density without sacrificing cycle life or calendar life of the battery.”
The cathode side is where lithium-ion batteries really taste the rainbow. A number of different chemistries are in common use today, and this is what produces most of the variations in battery characteristics. There’s lithium in the form of cobalt oxide (LCO), manganese oxide (LMO), iron phosphate (LFP), nickel manganese cobalt oxide (NMC), and nickel cobalt aluminum oxide (NCA). If you shop for cylindrical lithium-ion cells (such as the common 18650 cell that looks like a bigger AA battery), you’ll find these acronyms can explain why their charge capacities vary.
LCO batteries have very high energy density but a limited cycle life, and they're commonly found inside laptops and phones. LMO batteries can better handle high rates of charge and discharge; these are already likely in your power tools. The other three are the stars of electric vehicles, which prioritize cycle life and cost. Tesla has mostly opted for an NCA chemistry, while NMC is the most common in other brands (though LMO appeared in early models). LFP batteries have a lower energy density but better stability and longevity, in addition to high discharge rates, making them a good option for stationary grid storage batteries or shorter-range vehicles.
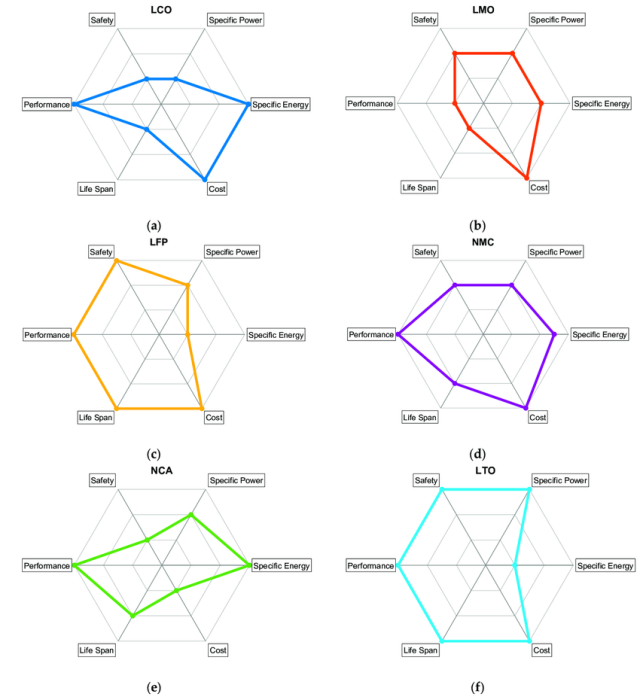
Each of these chemistries has evolved over time. “The cobalt oxide itself has gotten better and better and better, especially in the last ten years,” Srinivasan said. “We’ve been doing things like coating the surface of the cobalt oxide, changing what the electrode and electrolyte sees, minimizing the reactions that we don’t want, and ensuring that the reactions that we do want are the ones that occur. Ten years ago, I used to think that we are capped out on cobalt-oxide-based cells. Well, guess what, in the last ten years we’ve always found a way to make it better and better and better and get a little bit more every year.”
For nickel manganese cobalt oxide (NMC) cathodes, the recipes have changed in a pretty straight-forward way. An equal-parts chemistry labeled NMC111 or NMC333 has long dominated—cobalt helps with stability, but it's the highest-cost ingredient (in addition to human rights problems). Lower-cobalt formulations like NMC622 and NMC811 are on the upswing because they are both cheaper and have significantly higher energy density.
“But you need to solve some of the basic problems of high-nickel materials,” said Jansen, “and that’s when they start putting coatings on the cathode particles that try to keep the structure together so it doesn’t decompose with repeated cycling.”
The truth is out there
So where’s the proof that all this has been going on behind the scenes? If you look, the data bears out a number of trends. Energy density has a prominent trend. The original commercial lithium-ion battery, produced by Sony in the early 1990s, had an energy density of under 100 watt-hours per kilogram. That number has climbed over time, with the familiar cylindrical 18650 cells on the market hitting 200 watt-hours per kilogram by 2010. According to BloombergNEF, batteries used in electric vehicles have gotten as high as 300 watt-hours per kilogram in the last couple of years.
That has been easy to see if you’ve followed EVs at all, as the early options had nowhere near the range of what we see today. The first Tesla Model S offered about 210 miles of range, while it can now be purchased with up to 390 miles. The first Nissan Leaf could go about 75 miles, while a 2020 model can go 225 miles.
That’s not entirely down to increased energy density in the battery cells, of course. There are other variables, like the efficiency of the vehicle and the number of cells in the pack. That’s part of what makes it hard for consumers to notice whether the cells themselves have changed.
The complexities are apparent if you look at phones. One could compare stats on battery life of phone models over the years, and perhaps even energy capacity numbers for their batteries. But did the capacity increase because the cells became more energy dense, or because the manufacturer managed to squeeze a slightly larger battery in the case? Battery life isn’t a reliable indicator, either, because phones with more powerful hardware could have a larger power draw than their predecessors. On the flip side, software improvements for power efficiency could get you more life out of the same battery.
I've got a personal interest in cameras. I recently bought a new one to replace a decade-old DSLR of the same brand. The size and shape of the lithium-ion battery remains identical, but the new one has a capacity of 1900 milliamp-hours while the old one was 1500 milliamp-hours. That’s an increase of 27 percent. (And it’s not the biggest available currently.)
Does that mean the new camera lasts 27 percent longer than my old one? Far from it! I can expect to shoot fewer than half as many photos before needing to recharge. The new (mirrorless, if you’re hip to photography lingo) camera shoots at higher resolution, has a more active auto-focus system, contains a higher resolution and brighter screen, and what used to be a passive optical viewfinder is now a second, tiny screen—all adding up to a comparatively ravenous appetite for electrons.
- Lithium-ion batteries have come a long way from their origins in the early '90s.
- Energy densities for multiple chemistries are on the rise.
- Falling battery costs have pretty consistently beat forecasts.
- It's no surprise that EV range is increasing.
But there's also a big trend that has little to do with performance. The cost of lithium-ion batteries has fallen dramatically—with huge effects on electric vehicles. A recent study noted that “the real price of lithium-ion cells, scaled by their energy capacity, has declined by about 97 percent since their commercial introduction in 1991.” The early lithium-ion cells in the 1990s were around $3,000 per kilowatt-hour. By the early 2000s, that was nearer to $500 per kilowatt-hour.
In terms of electric vehicles, BloombergNEF estimates that the average price of a complete battery pack was about $1,180 per kilowatt-hour in 2010. By 2020, it was down to around $130 per kilowatt-hour. Ultimately, this is what makes it possible to produce a car with 300-mile range that someone not named “Jeff Bezos” can plausibly afford.
There’s also more to a battery than the simple sum total of electrons it can push before the meter reads zero. Unlike internal combustion vehicles, where engine performance more or less maps to “how much of a dangerous idiot can I be on the road?”, battery performance relates to charging as much as discharging. (Ars Automotive Editor Jonathan Gitlin is now free to challenge me to a duel.) Fast charging is key to making electric vehicles convenient for more use cases, so this is another priority for battery development.
Faster charging depends on everything from cell design to pack layout and temperature management to charging station infrastructure. Manufacturers have to understand how their batteries respond to various levels of fast charging and settle on a safe and reasonable trade-off of life cycle degradation for the convenience of a quick top up.
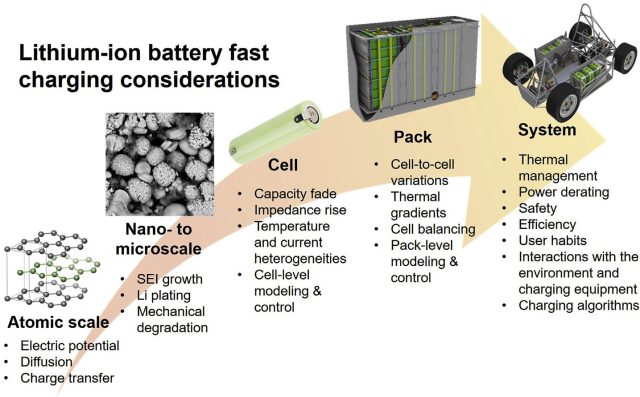
Industry standards for charging stations (including plug shapes) have evolved over time, pushing to higher maximum charge rates. A charger in your garage can push a few kilowatts of AC power, which the vehicle’s charging system converts to DC on its way into the battery. Fast charging stations deliver much more power, converted to DC on the other side of the plug so you can exceed what the vehicle’s charging system can manage. Earlier vehicles and stations could push charging to 50 kilowatts, while Tesla’s superchargers initially went as high as 150 kilowatts. The newest Tesla superchargers can reach 250 kilowatts, while new Electrify America stations are capable of 350 kilowatts—assuming a vehicle comes along that can take it.
A Tesla Model 3 can hit peak charge rates around 250 kilowatts, and a Porsche Taycan can nudge a little higher. But other vehicles are generally a little more conservative, with the Chevy Bolt limited to 50 kilowatts and the new Volkswagen ID.4 capable of 125 kilowatts.
In general, though, you can charge a vehicle faster today than you could 10 or even five years ago, and companies are focused on pushing these numbers higher. This can’t all be credited to changes in the battery cells, themselves, but they're far from irrelevant here.
The electrons must flow
If progress has been steady all this time, there’s obviously more on the way (stay tuned on that). First, there will be more in the incremental vein, as we have yet to reach the theoretical limits of lithium-ion. For example, when Tesla laid out its plans last year, there were many little things that added up to a hoped-for increase of around 50 percent in vehicle range and decrease of around 50 percent in per-kilowatt-hour cost. That came from cathode material tweaks, a high-silicon-content anode, a larger cylindrical cell design, a redesigned battery pack, and new manufacturing methods. Who knows how long it will take for all this to materialize, though Elon Musk claimed it would only be around three years.
Beyond the incremental, less predictable battery revolutions are also coming to placate the impatient. (Just don’t expect flying cars to be close behind.) The race to develop solid-state batteries that ditch liquid electrolytes—and perhaps also the bulk of the anode—seems to be heating up. That could bring sudden improvements in safety, longevity, or energy density.
Researchers have also long been chasing lithium-air batteries that could realize a huge jump in energy density. And beyond lithium, there are other entirely different chemistries in development out there. At some point, one of them should click for one application or another.
Lithium-ion or not, an explosion of grid-scale battery installations is coming as prices continue to fall. The nascent art of lithium-ion battery recycling is also sure to mature and expand, improving the sustainability of these batteries by recovering and resetting their chemical building blocks.
Adopt cold-fusion-like skepticism of any of these future-looking statements as you please, but today’s batteries aren’t those of 20 or even 10 years ago. The same thing is bound to be true in another 10 years—even if that progress doesn’t come in a single, giant leap with global fanfare.
"five" - Google News
May 24, 2021 at 06:15PM
https://ift.tt/3wuA6bn
Eternally five years away? No, batteries are improving under your nose - Ars Technica
"five" - Google News
https://ift.tt/2YnPDf8
https://ift.tt/2SxXq6o
No comments:
Post a Comment